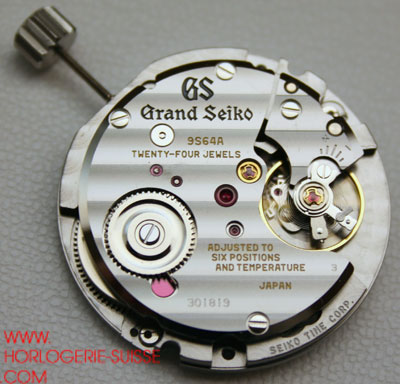
Au terme d’une visite de manufacture et d’initiation de cinq jours, Seiko a révélé certains de ses secrets.
Fabrication, horlogerie, finitions, habillage, culture et habitudes, voici le compte-rendu d’une épatante découverte : l’horlogerie mécanique à la mode japonaise.
Elle est considérée avec méfiance, voire avec une hauteur teintée de nationalisme. A la différence de l’industrie helvétique, constellation d’acteurs de tous types, l’horlogerie nippone est quasiment personnifiée par une seule société : Seiko.
Lors d’une visite de manufactures de plusieurs jours, cette maison présente ses différents visages, et ils sont nombreux. De la montre à quartz à 200 frs jusqu’à la répétition minutes fabriquée à cinq exemplaires par an, le groupe offre une pléthore de produits, fabriqués selon des approches très différentes et cohabitant sous une même enseigne. Cette diversité est le produit de l’histoire de Seiko. Créateur de la première montre de poignet à quartz, l’Astron de 1968, la marque incarne encore la force de la révolution technologique qu’a été en son temps le régulateur piézo-électrique miniature.
Précurseur de la montre électronique, de la montre digitale, Seiko continue à produire des mouvements par dizaines de millions. Issus de chaines de production entièrement automatisées, ils constituent encore aux yeux du groupe une source de fierté. Le quartz est encore chez Seiko un produit d’avenir, au contraire de la Suisse. Le groupe a bâti sa prospérité sur cette technologie, qu’il est l’un des derniers à encore faire évoluer. Ainsi, le modèle Astron de 2012 est-il à quartz, à recharge solaire, et à ajustement horaire par satellite. Son antenne accroche le signal GPS venu du ciel et se synchronise automatiquement.
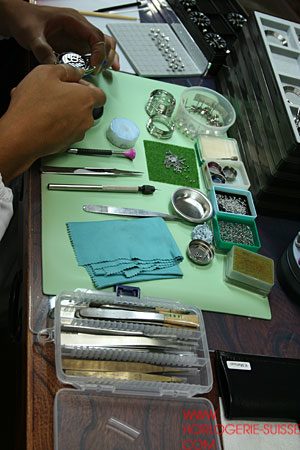
Marque, groupe, pays
La raison d’une telle variété d’approche est aussi dû au fait que Seiko est non pas une simple marque, mais un groupe. Au Japon, il est constitué de 12 marques dont seule une poignée est commercialisée ailleurs, et encore est-ce beaucoup en Asie. Le nom sur lequel le groupe compte pour exister dans l’horlogerie mécanique se nomme Grand Seiko. S’il s’agit d’une véritable institution au Japon, d’une marque ancienne, encore relativement inconnue en dehors d’un cercle d’amateurs, elle incarne tout le savoir-faire horloger du Japon.
Née en 1960, elle a alimenté le pays en montres mécaniques de haute qualité pendant des décennies. Elle a cherché à rivaliser avec la Suisse de toutes ses forces, par le même processus qui a fait la puissance industrielle du pays : copier, apprendre, améliorer, vaincre. Après avoir disputé les places d’honneur de la chronométrie aux suisses pendant le plus clair des années 60, c’est finalement avec la rupture technologique du quartz que Seiko l’a emporté. Mais le savoir-faire des montres mécaniques n’a jamais été abandonné et c’est Grand Seiko qui est chargé de le perpétuer. Pour ce faire, deux sites industriels l’alimentent en composants, mouvements et produisent des montres.
Mécanique
Seiko Instruments Inc. est situé dans le nord du pays, à Morioka. C’est ici que sont produits les mouvements mécaniques Seiko haut de gamme. D’un côté, des milliers de mètres carrés consacrés à la production de mouvements à quartz par dizaines de millions. De l’autre, l’horlogerie mécanique, goutte d’eau manuelle dans un océan industriel. Un atelier d’étampage à sec et décolletage est situé à quelques mètres d’un atelier de roulage. La porte suivante cache un atelier de décoration et de redressage. Partout, il y a dix fois plus de machines que d’homme.
Le parc industriel est d’une taille affolante, les surfaces occupées aussi. L’explication est simple : chaque machine effectue une tâche. On ne la reprogramme pas, elle ne refroidit pas, elle est toujours calée et donc efficace. L’idée de l’investissement sous-jacent donne le tournis, la capacité de production aussi.
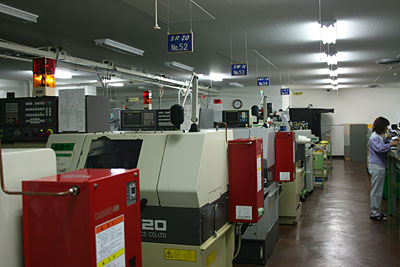
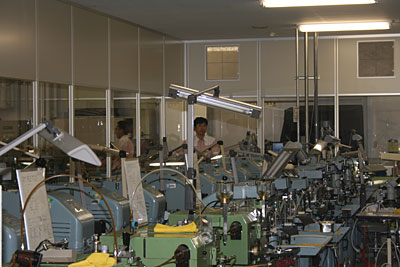
L’atelier
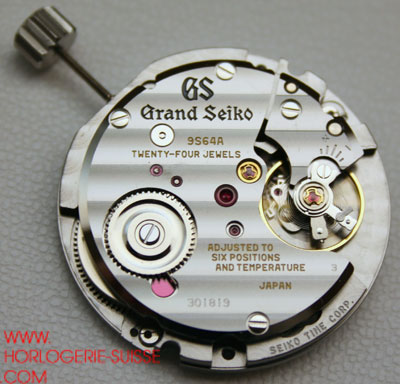
Après avoir passé un sas à différentiel dépression qui pompe les poussières, on pénètre dans le T1 : le Shizuku-Ishi Watch Studio. À droite, le garnissage et l’huilage sont totalement manuels. A gauche, les photos sont interdites. Une machine faite sur-mesure, couplée avec deux OmegaMetric d’antan, produisent du spiral à la chaîne. Le Graal horloger est ici fabriqué automatiquement, avec une intervention humaine minimale. L’alliage est maison, il se nomme SPRON 610. Les roues d’échappement sont en nickel, façonnées par MEMS, un système de d’électro-lithographie de précision de type LIGA.
Seiko produit des assortiments peu chers, qui lui permettent de régler les montres de sa gamme Grand Seiko à -3 + 5 secondes par jour sans peine. C’est ici que les spiraux sont montés sur les balanciers, équilibrés et ajustés, le tout à la main. Ils sont ensuite intégrés dans la gamme 9R de calibres mécaniques. La gamme est courte et visible sur le site ww.seiko.fr.
Sa ligne directrice est : automatique, efficace et de faible complication. L’atelier a une capacité d’assemblage de 10 000 montres par an, bien moins que la capacité apparente des salles de machines qui l’approvisionnent. Mais les processus sont manuels, très peu automatisés ou assistés de machines. Le garnissage et l’huilage par exemple, sont effectués par des opérateurs de niveau moyen de qualification, mais à la main.
Ambiance
L’environnement de travail est comme le reste, presque comme en Suisse mais en fait totalement différent. Les établis sont fabriqués sur mesure pour les opérateurs (et non pas juste réglables en hauteur) en Kaïki, un orme rouge et veiné. Les caissons sont décorés de coins en métal ouvragés. Les fauteuils sont des modèles ergonomiques de chez Herman Miller, le leader en la matière. Tout le monde travaille à la binoculaire. Pas de micros, la recherche de précision passe avant celle du confort de posture. L’environnement est climatiquement contrôlé et la traque à la poussière commence dès l’entrée du bâtiment où, Japon oblige, on retire ses chaussures pour passer des chaussons dignes d’un hospice de retraite est-allemand. On enfile ensuite une charlotte jetable encore moins gracieuse que le bonnet de pâtissier que portent à longueur de temps les horlogers. Leurs bouts de doigt sont couleur latex, et certains les portent par dessus des gants en coton (pour éviter l’effet raisin sec….). Quant on élimine le boudin excédentaire qui coupe la circulation…on vous propose un autre bout de doigt.
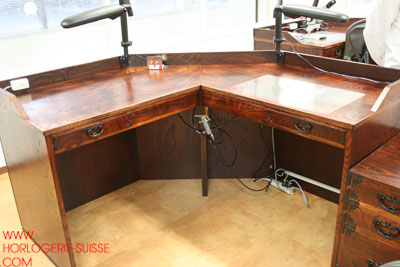
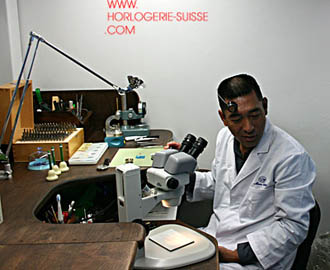
Habitudes
La journée de travail commence à 8h15 pile et se termine à 17 heures, tout aussi précises. Trois fois par jour, une petite musique de fond remplit les ateliers. Tout le monde s’arrête de travailler et se lance dans quelques minutes d’exercice physique, petite gymnastique obligatoire et hygiénique. Le staff est mixte, de tous les âges et face à des visiteurs en nombre et assez inquisiteurs, très concentrés pour éviter les questions. Les machines sont à 90% japonaises, mais les outils peuvent être suisses, Bergeon se révélant incontournable où que l’on aille. Le reste des mouvements mécaniques est fabriqué à Singapour. Ils animent une sous-marque qui n’est plus distribuée en Europe, Seiko 5, très abordable et prisée des amateurs d’horlogerie simple. On nous assure qu’aucun composant touchant aux montres mécaniques n’est fabriqué ou assemblé en Chine.
Le moteur hybride
L’autre pilier de l’offre de Grand Seiko se nomme Spring Drive. Ce système hybride électromécanique est l’association d’un régulateur à quartz et un rouage mécanique. La transmission entre les deux se fait par une roue dont la vitesse est régulée électromagnétiquement, dont la rotation est transmise directement à la trotteuse des secondes. Lisse et sans à-coups, elle est sensée refléter la nature du passage du temps : constante, fluide. Spring Drive est un tout autre monde. Il règle à une précision de + ou – 1 seconde par jour, contre une exigence de -3 +5 pour les montres mécaniques. Tous les mouvements Spring Drive sont assemblés à Shiojiri, près de Nagano, dans le centre du pays. Cette région est spécialisée dans la mécanique de précision comme certaines vallées suisses le sont dans le décolletage. L’usine appartient à Seiko Epson, cœur d’un empire industriel diversifié, où la goutte d’eau qu’est l’horlogerie haut de gamme rejoint l’océan informatique d’Epson. Elle est divisée en trois parties. Le studio Takumi assemble et emboîte les calibres Spring Drive. Les processus d’assemblage sont moins léchés, moins soignés. Les kits de mouvements sont livrés en vrac, les pièces non visibles se touchent et se rayent. Celles livrées à l’œil sont mieux traitées. Le pragmatisme règne en maître, et en premier lieu celui qui a amené à la conception (longue et douloureuse) de Spring Drive. On fabrique aussi le calibre 9F, quartz de haute précision, objet de fierté pour son micro moteur sans recul, son rattrapage de jeu d’engrenages et sa date qui saute en 1/2000é de seconde.
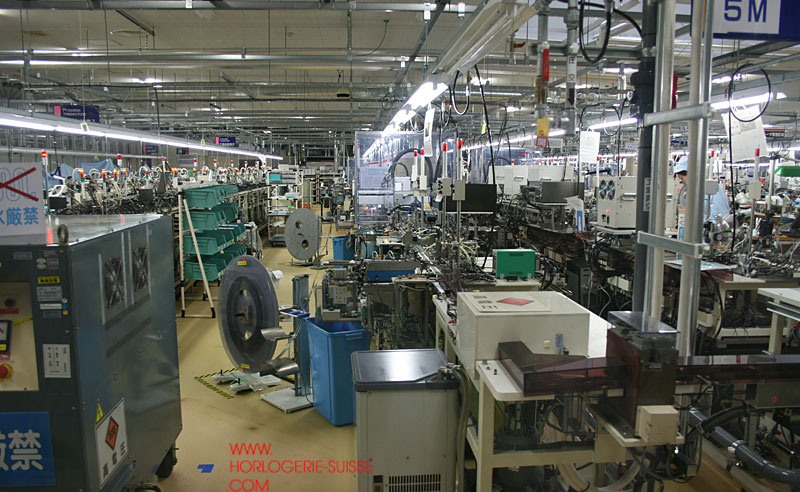
Placard à sonnerie
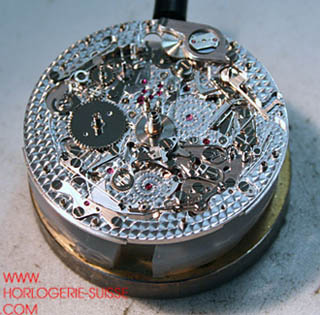
Le second studio est dédié aux pièces joaillères, peu exportées. Le troisième est microscopique. Il faut descendre un escalier et ouvrir une petite porte pour découvrir l’atelier des sonneries. En 2006 et sous la marque haut de gamme Credor, Seiko présente une sonnerie au passage, dont la musique provient d’un timbre en forme de bol d’airain.
Provenant de l’univers de prêtres bouddhistes, la cloche Orin a une sonorité extraordinaire claire, longue, une petite merveille. En 2012, la marque a récidivé avec une Répétition Minutes décimale (elle sonne les heures, les dizaines de minutes, puis les unités des minutes), entraînée par un Spring Drive exemplairement silencieux. Trois hommes travaillent à plein temps dans ce placard à balais en sous-pente. Cet espace presque suffocant les soude, les met à part, orfèvres du temps dans un environnement productiviste.
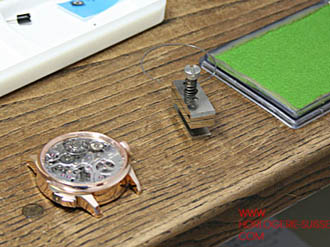
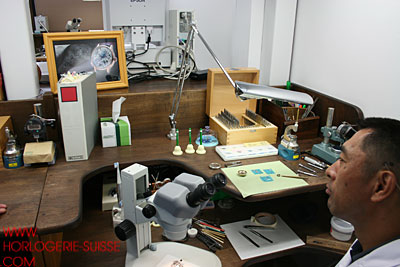
Habillage
C’est également dans cette usine que sont fabriqués les cadrans, aiguilles et boîtes Grand Seiko. L’esthétique de la marque est relativement uniforme et la gamme étroite. La variété des opérations est donc limitée. Une seule forme d’aiguilles, avec deux variantes de diamantage, des cadrans majoritairement gris soleillés, un système de décalque par tampon encreurs classiques, on pourrait être en Suisse. Mais le polissage des boîtes est un travail tout à fait unique, qui suit une organisation et des directives très strictes. Un dégrossissage au jugé est toléré pour les montres de base. Les modèles haut de gamme et les boîtes en or passent au polissage tenues par des bras qui ressemblent à ceux des tailleurs de diamants. Ils sont posés sur des rails qui les guident et travaillent sur des angles au degré près. La minutie de l’opération fait passer le Poinçon de Genève pour un jeu d’amateur. Toutes passent ensuite à l’étape du Zaratsu, un type de polissage qui donne un brillant tout particulier aux carrures de boîte. Encore une fois, les quantités hommes/machines sont surprenantes.
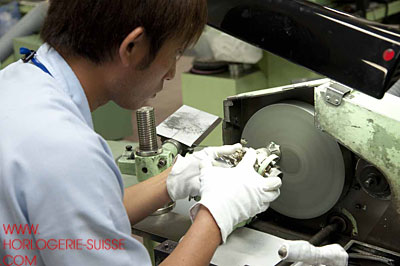
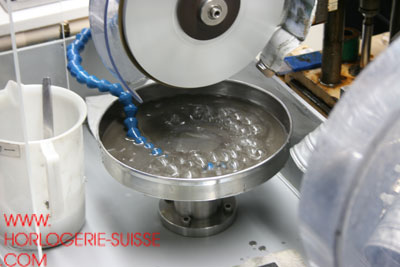
Un monde à part
L’horlogerie japonaise vit à distance de l’helvétique. Elle lui a emprunté ses principes de construction, ses méthodes, ses ambitions. A l’heure où la montre mécanique à retrouvé tout son pouvoir de séduction, Grand Seiko revient sur la scène internationale. Avec prudence, la marque veut sa part du gâteau. Pour cela, elle propose des produits d’une sobriété exemplaire. Que le monde soit à la peine pour comprendre le principe de Spring Drive, que ses marques soient encore perçues comme bas de gamme ne leur pose pas de problème. L’état-major de Seiko progresse avec lenteur et méthode. Un renouvellement des complications, une forme d’ouverture sur les besoins d’un public international devrait les aider, le management étant encore très nippo-centré. Si les mécanismes sont fabriqués très manuellement, avec pragmatisme et en séries importantes, le soin réel apporté à l’habillage est un cran au-dessus. Il contribue à doter les montres Grand Seiko d’un rapport qualité/prix franchement excellent.
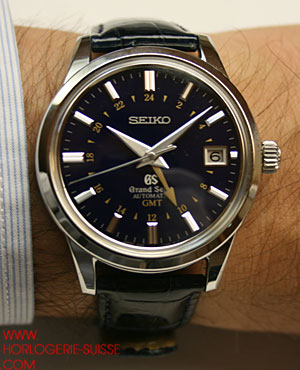
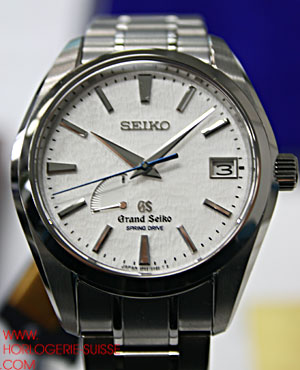
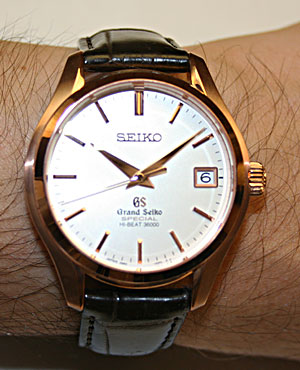
Par David Chokron